コラム”Ecoものづくり情報”
コラム”Ecoものづくり情報”
コラム”Ecoものづくり情報”
■ 改善の4原則=ECRS
Ecomo
Ecology&Economy manufacture optimization supporter
"Ecoものづくりサポーター”
エコモ研究所 宇田英夫
〒602-8148 京都府京都市上京区丸太町通堀川西入西丸太町185番地
京都二条ハイツ703
TEL 075-756-3353
携帯 080-3032-7213
Email ecomouda@ab.auone-net.jp
HP http://www.ecomouda.com
■取組改善革新例
工場の『診える化』と『最適化』Eco活動でお伝えしたいことは、単に工場での「見える化」をすることだけではなく、「見える化」を進化させて『診える化』としていくことの大切さでした。『診える化』の意味が少しずつですが感じることができ、今までには、知らなかとこと、感じなかったこと、解からなかったことを感じるようになっていったのです。
これから、その省エネ環境Eco活動の改善事例で学んだ、工場の『診える化』と『最適化』について詳しくお話をしたいと思います。ものごとの捉え方や考え方を大きく変えることに至った、学び・教訓の取組事例ですが、お許しいただき紹介をさせていただきます。
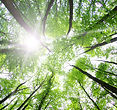
工場の『診える化』
■工場の『診える化』
先ず、取組を始めるにあたりクリーンルーム内の各設備に電力モニタと生産現場の環境と状態をリアルタイムに計測できる状態センサを設置し、1分毎にセンシング(計測)していきました。
その電力と生産現場の状態(パーティクル・温湿度・エアー流量圧力・差圧)をセンシングし、一分毎のリアルタイムデータを表示監視ができる「電力環境監視システム」の開発を行なっていきました。
その「電力環境監視システム」は、電力・環境の改善を進めるために、生産現場の各装置電力の使用量と状態の変化を表示して、その変化から改善へのコミュニケーションを図る「省エネ環境コミュニケーションボード」として活用運用を進めて行ったのです。
後に、この「省エネ環境コミュニケーションボード」は、“環境あんどん”と命名されて、現在はオムロン株式会社にて標準ソフトとして市販化されています。

クリーンルームの省エネ環境活動
■クリーンルームの省エネ環境活動
『診える化』と『最適化』について、学んだクリーンルームの省エネ環境取組を紹介します。
そのクリーンルームの省エネ環境改善は、小さなクリーンルームの事例ですが、半年間で、様々な改善活動ができて、クリーンルームの環境改善と合せて、クリーンルームで生産する製品の原単位電力を半減する省エネルギー活動をすることになりました。
“電力環境診える化システム=環境あんどん”にて、電力やパーティクル量(パーティクル量とは、0.5ミクロンの微小チリ・ゴミの量が1キュービックフィート当たりに浮遊している数のことです)を1分毎に測定し続けていると、今まで見ることの無かったクリーンルームのチリ・ゴミの変動をリアルタイムグラフとして見ることができたのです。
その異常が起こる動作や作業および状況や状態のヒントから、異常が起こらない様な動作・作業と状況や状態にしていくことで、パーティクルがでないように抑える対応策を考えて、改善を進めていくことができるようになっていきました。
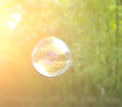
『真の省エネ』活動
■『真の省エネ』活動
クリーンルームには、室内のパーティクル量を減らすために、空気をHEPAフィルタにて濾過してきれいな空気を循環送風するファンフィルターユニット(クリーンエアー装置・クリーンユニット)を7台連続稼働していました。
『診える化』により、クリーンルームのパーティクル量の異常や揺らぎの状態や状況を知って、そのパーティクル量を減らす状態や状況へとしていく改善がどんどんと進んで行きました。
そして、クリーンユニットを常時最大風量の連続強運転から、弱運転や7台の内の一部を運転停止できるようになり、必要なときに必要なファンフィルターユニットを運転する省エネ自動運転を行うようにして、ファンフィルターユニット電力は、従来に較べて40%の電力低減を果たすことができました。
「生産現場を良い状態や良い状況にするためにエネルギーを使用しているのですが、『真の省エネ』とは、エネルギーを使って生産に関わることを良い状況・状態をつくりあげるのでは無く、エネルギーを使わざるを得ない要因・因子を知って、その要因・因子を少なくすることや、無くしていくことが、エネルギーを大切に使うこととなり、更に、悪くなる要因・因子が少なくなっているのですから、現場は良い状況・良い状態となって、エネルギーを減らしていくことができる「真の省エネ活動」と言うことでした。
「良い状況・状態をつくっていれば必要なエネルギーは最小になるのです。先ずは、良い状態・良い状況をつくることが省エネ活動の本質なのです。」
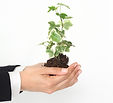
印刷工程の『最適化』
■印刷工程の『最適化』
「印刷工程をキレイにすることは、その印刷を行っているところ、電子基板をはんだ印刷する箇所がキレイになっていることではないか」と思い、印刷機を大きなブース化から、できる限り印刷工程を覆っているブースを小さくして、キレイな空気を送れるようにファンフィルターユニットのクリーンエアーを印刷機内部に案内筒に通して入れるようにしていきました。
そうすると印刷機内部はクリーンエアーで満たされて、空気をキレイにすることができるようになり、印刷工程のブースを1/2にすることができました。そうすることで、ファンフィルターユニット数は2台から1台へ、更に、冷風を送っているスポットクーラも2台を1台にすることができ、印刷工程のクリーン電力量を半減することができました。
そして、印刷工程内部の排気改善とクリーンエアー流入量を多くすることで、パーティクル量は最終的に、従来の5分の1に減らすことができたのです。
また、作業者の負担になっている1日に数十回行っている段取り変え時のカーテン開閉作業を何とかしてあげたいと思うようになり、クリーンエアーを印刷装置内に入れたことから、版替え時に印刷機前面の扉を開けても印刷機内部からクリーンエアーが逃げる量が多くなっていることで、外部からブース内へはチリ・ゴミが入り難くなっていたのです。そして、この工程・ラインで生産している電子基板生産の歩留り(品質)も良くなっていったのです。
省エネ・パーティクル量を低減する改善活動が、品質改善や段取り作業の生産性改善にも繋がり、安全で安心して現場の生産が進められたことで、工程を『最適化』することができると言うことでした。